For most of the country boating is in the deep freeze or at least curtailed due to winter weather, but we are all looking forward to warmer weather and the upcoming boating and fishing season, and that means this is a great time to review your boat’s safety gear, something that should be done on a regular basis. Yamaha always recommends safe and responsible boating practices, stressing the importance of having adequate safety equipment onboard and maintaining it in good working condition. With that in mind, let’s review the U.S. Coast Guard required safety gear for recreational vessels and what to look for to make sure it is in shape for the upcoming season.
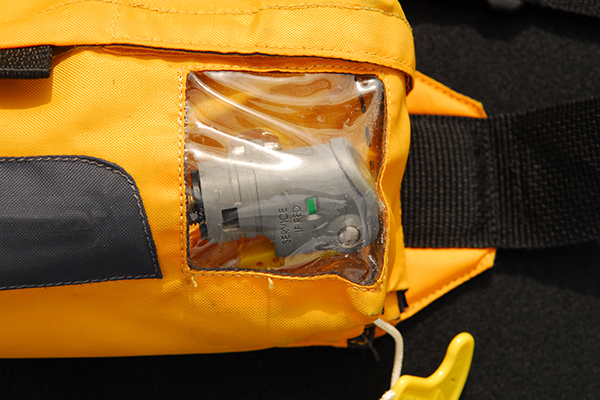
Personal Flotation Devices:
Starting this section with the ubiquitous personal flotation device (“PFD”) is appropriate because it is the most widely recognized piece of marine safety gear and, when worn, offers the most immediate lifesaving capabilities. Yamaha recommends that the operator of and all passengers on a marine vessel wear a U.S. Coast Guard approved PFD. The U.S. Coast Guard has PFD requirements for recreational vessels broken down into categories; for boats 16 feet and under (small), and boats from 17 feet up to 65.6 feet (large). PFDs are required for ALL vessels and fall into four types that can overlap in application. Boaters should also check state and local laws regarding PFD requirements.
Small vessels must have one approved Type I, II, III or V PFD for each person on board or being towed on water skis, wake boards or tubes. Large vessels must have one approved Type I, II, III or V PFD for each person on board or being towed on water skis, wake boards or tubes, and one throwable Type IV device.
Type I offers the highest degree of flotation and is recommended for open ocean, rough seas or remote waters where extended time in the water could occur while awaiting rescue. Type I is required for certain classifications of Coast Guard inspected vessels and all vessels that carry passengers for hire.
Type II, also called Near-Shore Buoyant Vests, are the most common type used for recreational boating activities. They are considered good for relatively calm near-shore and inland waters where the chance of a quick rescue is likely.
Type III is considered a Flotation Aid and designed to complement a specific specialized activity noted on the device such as water skiing, fishing, canoeing, kayaking, etc. They are recommended for calm, inland waters, or where there is a good chance of a fast rescue.
Type IV differs from the other types in that it is not worn but intended to be thrown to a person in the water. Large vessels are required to have at least one throwable flotation device onboard.
Type V is classified as a Special Use device designed for specific purposes that could include canoe/kayak vests, deck suits, or work vests for commercial vessels. In most cases they must be worn at all times for their
intended purpose.
There are two main variants of the five Types of PFDs; inherently buoyant which are made using some type of flotational foam, and inflatable. There is also a less common variant called a hybrid that combines both types of flotation. When checking your PFDs for serviceability all that is necessary for the inherently buoyant type is do a visual check to make sure the outer fabric, straps and fasteners are in good condition and that the foam has no indication of water intrusion. Cleaning the outer surface to prevent mold is a good idea at least once a year, more frequently if they are kept in a compartment where moisture is a factor.
Servicing inflatable PFDs is a bit more involved and should include a visual inspection before each use, a more involved bimonthly inspection that includes simple testing, and an annual inspection, according to Mustang Manufacturing, one of the largest manufacturers of marine safety and lifesaving equipment.
Before each use always check to see if the Inflator Status indicator is Green showing that the PFD will inflate upon activation and that the manual inflation pull is accessible. On a bimonthly basis perform an Oral Inflation Valve Test by fully inflating the PFD using the oral inflator tube and then holding it under water. If bubbles appear coming from the inflation tube, deflate it, and repeat the test. If bubbles continue, there is a problem with the valve requiring service or replacement. Then perform a general Leak Test by orally inflating the PFD until firm, then letting it sit for 16 hours. A PFD with a leak will not maintain its firmness and should be professionally repaired or replaced. Last, inspect the bobbin. Most automatic inflating PFDs use a bobbin activation system. The bobbin looks like a bright yellow “pill” with solid white powder filling it around the axis. When the white powder gets wet it instantly dissolves and activates a pin that punctures the CO2 cylinder inflating the PFD. Inspect the bobbin to make sure it is still intact and replace it if it looks in any way compromised.
On an annual basis, perform a thorough Visual Inspection, the Oral Inflation Valve Test, the Leak Test and clean the PFD to remove any dirt or possible mold that can form inside the unit if it is stored in a damp compartment. Check for corrosion and replace any corroded parts. Then record the date of the inspection and tests on the service record label using a permanent magic marker.
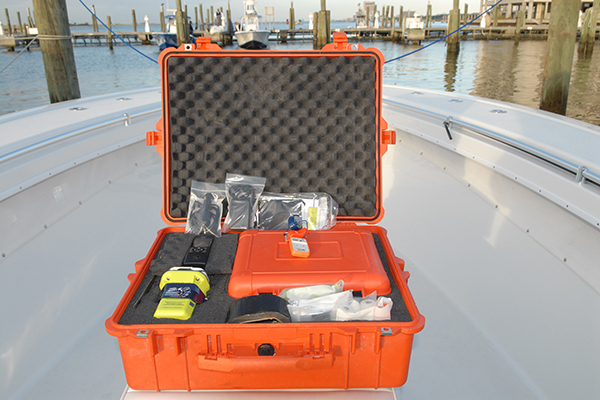.jpg)
Visual Distress Signals:
Visual Distress Signals, also called signal flares, are required on both large and small recreational vessels operating in coastal waters, the Great Lakes and aboard U.S. owned boats on the high seas. Small boats (>16 feet) are required to carry approved distress signals for night-time use while large boats must carry flares approved for both day and night-time use. Signal flares should be checked annually to see if they have reached the end of their life cycle. They are imprinted with an expiration date, usually about five years from date of manufacture. While older flares might continue to work beyond their life cycle, you must have fresh flares onboard. Expired flares can be cause for a citation if your vessel is boarded and inspected by state or federal enforcement agencies like the marine police or Coast Guard.
All the Whistles & Bells:
Every recreational boat less than 65.6 feet in length must carry an efficient sound producing device that can include an airhorn, electric horn, bell or whistle that is audible for one nautical mile. If you have a compressed air horn, check it annually for corrosion and make sure it toots when you press the button.
Fire Extinguishers:
A single Type B-1 approved portable fire extinguisher is required on all boats up to 26 feet with the following exceptions. Outboard powered boats less than 26-feet in length if the construction is such that it does not permit the entrapment of explosive or flammable gases or vapors, and if fuel tanks are not permanently installed. All boats between 26 and 40-feet must carry two Type B-1 or one Type B-II portable fire extinguisher and boats between 40 and 65.6 feet much carry three Type B-1 or one Type B-1 PLUS or one Type B-II fire extinguisher.
Fire extinguishers should be visually checked at least once a year to see if they have maintained the charge of fire retardant and propellant. A small gauge is located near the handle and trigger. The needle indicator will be in the green if properly charged. If it is in the yellow or red, it should be recharged or replaced.
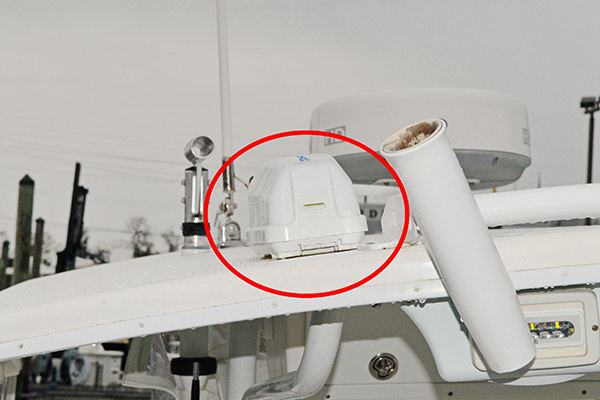.jpg)
Electronic Emergency Equipment:
One of the most basic pieces of electronic safety equipment on your boat is your VHF radio. Before leaving the launch ramp or your slip always request a radio check from another boater to be sure it is transmitting and receiving. Most VHF radios manufactured in the last decade include a red Distress Button utilizing a feature called Digital Selective Calling (DSC). When activated the radio sends out an automated May Day message including your current position over Channel 70, which is monitored under the Coast Guard’s Rescue 21 initiative. To work the radio must be interfaced with the boat’s onboard GPS unit and have been issued an MSSI registration number in advance. Both Boat US (www.boatus.com/MMSI/MMSI/Home) and the U.S. Power Squadrons® (www.usps.org/php/mmsi_new/) provide MSSI registration services. If you have not taken these critical steps, do so before you start this season as obtaining an MSSI number can take up to two weeks.
In recent years there has been a proliferation of more affordable emergency electronic signaling devices made available to the boating public that are game changers should an emergency occur, especially if you are unable to activate the Distress Beacon on your VHF radio. For boats operating on large bodies of water an Emergency Position Indicating Radio Beacon (EPIRB) is a smart addition to your safety equipment. An even less expensive alternative can be achieved with a Personal Locator Beacon (PLB), which operates in a similar manner to an EPIRB, but is registered to an individual rather than to a vessel and can be taken from one boat to another. All safety gear should be inspected at the very least seasonally and some items should be checked more frequently because they have expiration dates, batteries that require replacement, or components that have specific service intervals.
There are two basic types of EPIRB units for recreational vessels, Category I, which is automatically deployed by a Hydrostatic Release Unit (HRU) should the vessel sink, and Category II, which must be deployed manually. Both types will transmit a distress signal and GPS homing beacon to the international COSPAS-SARSAT® emergency response system and will initiate immediate emergency response by the closest rescue service.
EPIRBs that incorporate an HRU must be serviced or replaced every two years with inspection dates clearly marked on the HRU or on the unit. If it is within the expiration date take a close look at the release mechanism including any associated plastic bolts, rods, springs, or spacing washers to be sure they are free of corrosion, cracking or water intrusion. Any compromised parts should be repaired in accordance with the manufacturer’s recommendations. Check the expiration date of the EPIRB battery, which is located on the plate affixed to the unit. The battery must be replaced on or before the expiration date or if the unit is activated for any length of time. Battery life for most units is five years.
Every few months “self-test” the EPIRB following the instructions that came with the unit so that you do not transmit a false emergency signal. Most units have a clearly marked self-test switch that is spring loaded so it cannot be left on inadvertently draining battery power. When the switch is activated the unit will radiate a single burst radio wave coded so that it is ignored by the COSPAS-SARSAT® emergency system. A light on the unit will indicate that the test circuits are operating correctly.
PLBs are inspected and tested in much the same way as an EPIRB. A physical inspection of the unit should be conducted to be sure it is free of corrosion, water intrusion or damage and then check the battery expiration date on the unit’s ID plate. PLB batteries are good for five years from time of purchase and can only be replaced by the manufacturer or an authorized service center. Most manufacturers recommend conducting a self-test monthly. The test should be done in accordance with the manufacturer’s instructions so read the manual carefully as not all units have the same protocol.
Safe boating starts with your safety gear so always take it seriously. Make sure you have not only the equipment that is required, but the level of gear that will keep you and your guests secure should an emergency arise. While such emergencies are rare, the peace of mind is well worth the investment.
Back to Blue Life
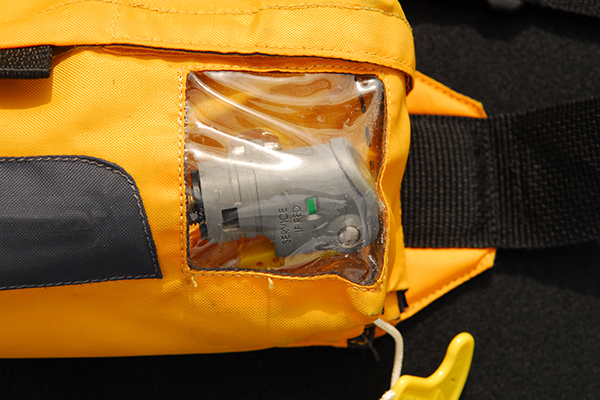
Personal Flotation Devices:
Starting this section with the ubiquitous personal flotation device (“PFD”) is appropriate because it is the most widely recognized piece of marine safety gear and, when worn, offers the most immediate lifesaving capabilities. Yamaha recommends that the operator of and all passengers on a marine vessel wear a U.S. Coast Guard approved PFD. The U.S. Coast Guard has PFD requirements for recreational vessels broken down into categories; for boats 16 feet and under (small), and boats from 17 feet up to 65.6 feet (large). PFDs are required for ALL vessels and fall into four types that can overlap in application. Boaters should also check state and local laws regarding PFD requirements.
Small vessels must have one approved Type I, II, III or V PFD for each person on board or being towed on water skis, wake boards or tubes. Large vessels must have one approved Type I, II, III or V PFD for each person on board or being towed on water skis, wake boards or tubes, and one throwable Type IV device.
Type I offers the highest degree of flotation and is recommended for open ocean, rough seas or remote waters where extended time in the water could occur while awaiting rescue. Type I is required for certain classifications of Coast Guard inspected vessels and all vessels that carry passengers for hire.
Type II, also called Near-Shore Buoyant Vests, are the most common type used for recreational boating activities. They are considered good for relatively calm near-shore and inland waters where the chance of a quick rescue is likely.
Type III is considered a Flotation Aid and designed to complement a specific specialized activity noted on the device such as water skiing, fishing, canoeing, kayaking, etc. They are recommended for calm, inland waters, or where there is a good chance of a fast rescue.
Type IV differs from the other types in that it is not worn but intended to be thrown to a person in the water. Large vessels are required to have at least one throwable flotation device onboard.
Type V is classified as a Special Use device designed for specific purposes that could include canoe/kayak vests, deck suits, or work vests for commercial vessels. In most cases they must be worn at all times for their
intended purpose.
There are two main variants of the five Types of PFDs; inherently buoyant which are made using some type of flotational foam, and inflatable. There is also a less common variant called a hybrid that combines both types of flotation. When checking your PFDs for serviceability all that is necessary for the inherently buoyant type is do a visual check to make sure the outer fabric, straps and fasteners are in good condition and that the foam has no indication of water intrusion. Cleaning the outer surface to prevent mold is a good idea at least once a year, more frequently if they are kept in a compartment where moisture is a factor.
Servicing inflatable PFDs is a bit more involved and should include a visual inspection before each use, a more involved bimonthly inspection that includes simple testing, and an annual inspection, according to Mustang Manufacturing, one of the largest manufacturers of marine safety and lifesaving equipment.
Before each use always check to see if the Inflator Status indicator is Green showing that the PFD will inflate upon activation and that the manual inflation pull is accessible. On a bimonthly basis perform an Oral Inflation Valve Test by fully inflating the PFD using the oral inflator tube and then holding it under water. If bubbles appear coming from the inflation tube, deflate it, and repeat the test. If bubbles continue, there is a problem with the valve requiring service or replacement. Then perform a general Leak Test by orally inflating the PFD until firm, then letting it sit for 16 hours. A PFD with a leak will not maintain its firmness and should be professionally repaired or replaced. Last, inspect the bobbin. Most automatic inflating PFDs use a bobbin activation system. The bobbin looks like a bright yellow “pill” with solid white powder filling it around the axis. When the white powder gets wet it instantly dissolves and activates a pin that punctures the CO2 cylinder inflating the PFD. Inspect the bobbin to make sure it is still intact and replace it if it looks in any way compromised.
On an annual basis, perform a thorough Visual Inspection, the Oral Inflation Valve Test, the Leak Test and clean the PFD to remove any dirt or possible mold that can form inside the unit if it is stored in a damp compartment. Check for corrosion and replace any corroded parts. Then record the date of the inspection and tests on the service record label using a permanent magic marker.
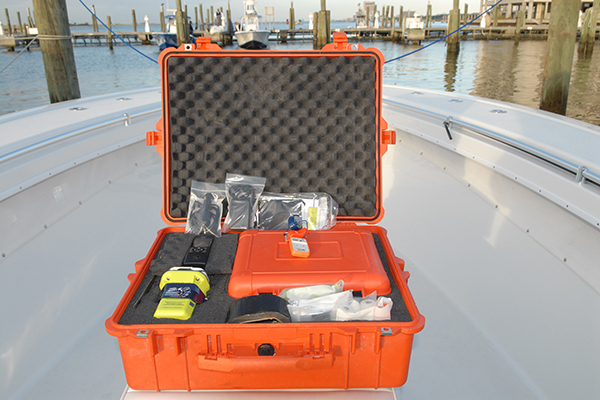.jpg)
Visual Distress Signals:
Visual Distress Signals, also called signal flares, are required on both large and small recreational vessels operating in coastal waters, the Great Lakes and aboard U.S. owned boats on the high seas. Small boats (>16 feet) are required to carry approved distress signals for night-time use while large boats must carry flares approved for both day and night-time use. Signal flares should be checked annually to see if they have reached the end of their life cycle. They are imprinted with an expiration date, usually about five years from date of manufacture. While older flares might continue to work beyond their life cycle, you must have fresh flares onboard. Expired flares can be cause for a citation if your vessel is boarded and inspected by state or federal enforcement agencies like the marine police or Coast Guard.
All the Whistles & Bells:
Every recreational boat less than 65.6 feet in length must carry an efficient sound producing device that can include an airhorn, electric horn, bell or whistle that is audible for one nautical mile. If you have a compressed air horn, check it annually for corrosion and make sure it toots when you press the button.
Fire Extinguishers:
A single Type B-1 approved portable fire extinguisher is required on all boats up to 26 feet with the following exceptions. Outboard powered boats less than 26-feet in length if the construction is such that it does not permit the entrapment of explosive or flammable gases or vapors, and if fuel tanks are not permanently installed. All boats between 26 and 40-feet must carry two Type B-1 or one Type B-II portable fire extinguisher and boats between 40 and 65.6 feet much carry three Type B-1 or one Type B-1 PLUS or one Type B-II fire extinguisher.
Fire extinguishers should be visually checked at least once a year to see if they have maintained the charge of fire retardant and propellant. A small gauge is located near the handle and trigger. The needle indicator will be in the green if properly charged. If it is in the yellow or red, it should be recharged or replaced.
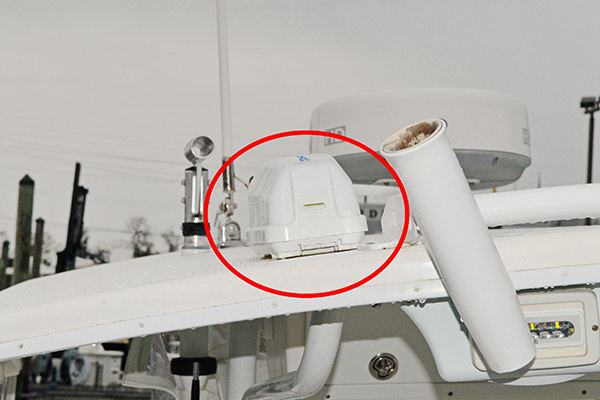.jpg)
Electronic Emergency Equipment:
One of the most basic pieces of electronic safety equipment on your boat is your VHF radio. Before leaving the launch ramp or your slip always request a radio check from another boater to be sure it is transmitting and receiving. Most VHF radios manufactured in the last decade include a red Distress Button utilizing a feature called Digital Selective Calling (DSC). When activated the radio sends out an automated May Day message including your current position over Channel 70, which is monitored under the Coast Guard’s Rescue 21 initiative. To work the radio must be interfaced with the boat’s onboard GPS unit and have been issued an MSSI registration number in advance. Both Boat US (www.boatus.com/MMSI/MMSI/Home) and the U.S. Power Squadrons® (www.usps.org/php/mmsi_new/) provide MSSI registration services. If you have not taken these critical steps, do so before you start this season as obtaining an MSSI number can take up to two weeks.
In recent years there has been a proliferation of more affordable emergency electronic signaling devices made available to the boating public that are game changers should an emergency occur, especially if you are unable to activate the Distress Beacon on your VHF radio. For boats operating on large bodies of water an Emergency Position Indicating Radio Beacon (EPIRB) is a smart addition to your safety equipment. An even less expensive alternative can be achieved with a Personal Locator Beacon (PLB), which operates in a similar manner to an EPIRB, but is registered to an individual rather than to a vessel and can be taken from one boat to another. All safety gear should be inspected at the very least seasonally and some items should be checked more frequently because they have expiration dates, batteries that require replacement, or components that have specific service intervals.
There are two basic types of EPIRB units for recreational vessels, Category I, which is automatically deployed by a Hydrostatic Release Unit (HRU) should the vessel sink, and Category II, which must be deployed manually. Both types will transmit a distress signal and GPS homing beacon to the international COSPAS-SARSAT® emergency response system and will initiate immediate emergency response by the closest rescue service.
EPIRBs that incorporate an HRU must be serviced or replaced every two years with inspection dates clearly marked on the HRU or on the unit. If it is within the expiration date take a close look at the release mechanism including any associated plastic bolts, rods, springs, or spacing washers to be sure they are free of corrosion, cracking or water intrusion. Any compromised parts should be repaired in accordance with the manufacturer’s recommendations. Check the expiration date of the EPIRB battery, which is located on the plate affixed to the unit. The battery must be replaced on or before the expiration date or if the unit is activated for any length of time. Battery life for most units is five years.
Every few months “self-test” the EPIRB following the instructions that came with the unit so that you do not transmit a false emergency signal. Most units have a clearly marked self-test switch that is spring loaded so it cannot be left on inadvertently draining battery power. When the switch is activated the unit will radiate a single burst radio wave coded so that it is ignored by the COSPAS-SARSAT® emergency system. A light on the unit will indicate that the test circuits are operating correctly.
PLBs are inspected and tested in much the same way as an EPIRB. A physical inspection of the unit should be conducted to be sure it is free of corrosion, water intrusion or damage and then check the battery expiration date on the unit’s ID plate. PLB batteries are good for five years from time of purchase and can only be replaced by the manufacturer or an authorized service center. Most manufacturers recommend conducting a self-test monthly. The test should be done in accordance with the manufacturer’s instructions so read the manual carefully as not all units have the same protocol.
Safe boating starts with your safety gear so always take it seriously. Make sure you have not only the equipment that is required, but the level of gear that will keep you and your guests secure should an emergency arise. While such emergencies are rare, the peace of mind is well worth the investment.
Back to Blue Life