A blend of automation and hands-on craftsmanship helps transform wax and metal into works of art called Yamaha propellers
When touring the new state-of-the-art Yamaha Marine Precision Propellers Inc. (YPPI) facility in Greenfield, Indiana, it’s hard to believe its origin can be traced back to a two-car garage in Indianapolis in 1969 where founder Jim Booe would repair props and also tweak them to make boats go faster. Later, he began making his own quality propeller and Yamaha Marine became one of his best customers. When Yamaha acquired Precision Propeller Inc. in 2008, it built on the work previously done and began a steady progression of modernization that took a quantum leap when it opened the Greenfield facility in July 2021. The Indianapolis plant is still operating and while the manufacturing — including the foundry — transitioned to the new facility, it’s still used to put the final touches on the propeller and prepare them for shipping.
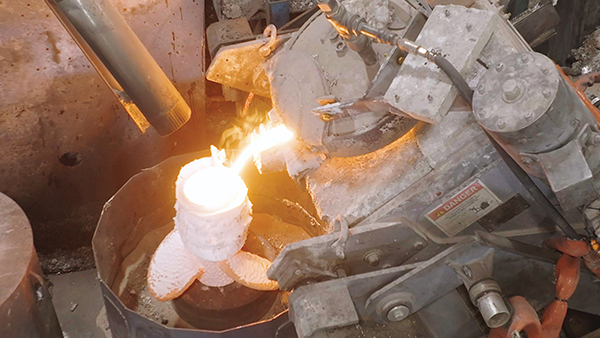
Robots do the Dirty, Difficult, Dangerous Jobs
The biggest change at the new $18 million, 55,000 square foot facility is its increased use of robotics to handle many of the potentially hazardous tasks such as pouring the 3,000-degree molten stainless steel from the crucible into the ceramic molds.
When most people hear the word robots, they assume the motivation to employ them is to replace human workers but in this case, it helped Yamaha up its production of propellers from 60,000 a year to more than 100,000 while achieving better tolerances that reduce waste and ultimately save the consumer money. Instead of laying off employees, Yamaha has been hiring more workers and operates 24 hours a day, five days a week, cranking out 300 different models of propellers. YPPI General Manager Batuhan Ak explains the other motives for switching some processes to automation, “The whole plant here was built with the philosophy of eliminating the 3Ds. We wanted to get rid of the difficult jobs, the dirty jobs and the dangerous jobs.”
Looking at just the pouring process illustrates how greater efficiency is achieved with the automated process. Previously, YPPI used two induction furnaces. One held 150 pounds of molten stainless steel while the smaller one held 65 pounds. Between the two, there was enough liquid metal to make seven propellers at a time. For smaller propellers, when the metal was hot enough, two silver-suited workers would lift a crucible filled with molten metal and manually pour it into the ceramic propeller molds. After which, another insulated employee would move the glowing mold and place it on a cooling rack where an open-ended barrel would be placed over it to contain the radiant heat to foster a consistent cooling environment. The larger props were filled with a manually tiltable crucible. Then, there would be a 15-minute reset while metal ingots were loaded and heated to 3,000 degrees.
The new auto-pour system holds several thousand pounds of molten stainless steel alloy and as the level goes down, more can be added without pausing. The new metal takes about 15 seconds to come up to the correct temperature so it can continuously operate. The system is also safer for employees since it eliminates manual pouring for the Yamaha props.
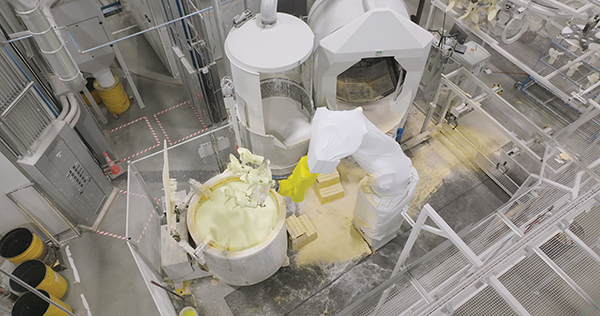
The Ancient Art Made Modern
Only stainless steel propellers are made and finished at the two Indiana facilities and the construction technique used is similar to the lost wax process Egyptians used 5,000 years ago to make jewelry. Although robotics makes sense for some tasks, many of the jobs require skilled workers with many years of experience to accomplish. The manufacturing process starts by injecting melted wax into an aluminum mold where it’s put under 200 pounds
of pressure to help fill the voids and ensure the perfect density of the hubs and blades, which are molded separately. After the wax cools, the mold is cracked opened and the formed components are inspected and any extraneous wax remnants are scraped off.
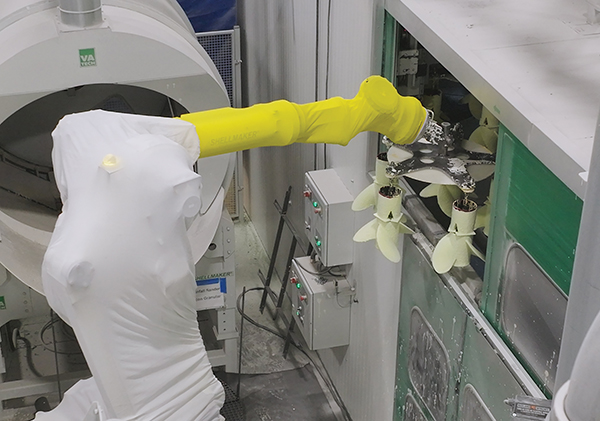
It Takes a Very Skilled Village
The blades are then joined to the hub and this is an especially critical step that requires a skilled hand. The assembler uses a soldering iron to join the base of the blade to the hub but if it’s applied a fraction of a second too long the blade or hub will be ruined. The positioning of the blades onto the hub must be perfect. When the blades are in place, black goop is applied to the base and it’s smoothed with a heated ball and the excess is scraped off. If the seams aren’t perfect, it will show up when the metal is poured and the propeller will have balance issues and could be scrapped.
Next, a pour cup is attached, which acts as a funnel, and the assembly is given several baths to clean the surfaces inside and out. The first appearance of robots appears at the dipping station where five wax propellers at a time are dipped into a primer slurry and turned and rotated like an amusement park ride to ensure an even coating before being given a zircon flour (milled sand) shower to start the build-up process of creating a ceramic shell. Four more layers of slurry and silica sand are added to increase thickness with periods of drying in between and after. This process used to be done by hand, which could cause inconsistencies and could take days but now can be done in 24 hours.
The dried ceramic shell still contains the wax, which must be melted away in an autoclave to create a void where the molten metal will fill. Then the ceramic mold is heated in preparation for the pouring.
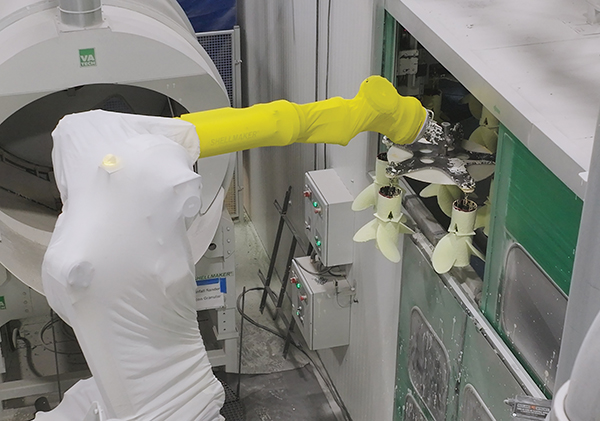.jpg)
It’s 3,000 degrees but it’s a Dry Heat
Next, comes the automated pouring sequence previously described. The entire process is monitored by computers and the progress of the line is displayed on giant screens throughout the plant including the reception area. This allows everyone to observe, at a glance, if progress is keeping pace with projections and where problems may exist. It even shows the angle of the last pour from the crucible, which lets supervisors know how much molten metal is remaining. They can even monitor the process remotely by smartphone to always stay in the loop.
Then, the newly poured propellers are sent to the cooling station and later the ceramic shell is removed by pneumatic hammering before being sand-blasted to remove any remnants, and then the pouring cup is cut off. According to Ak, the manual sand blasting station is one of the next scheduled processes to be automated since it’s one of those dirty jobs they are seeking to eliminate.
What’s left is a grey propeller with a dull finish since it’s covered with a coat of “free iron” which will be removed by abrading it with stainless steel balls.
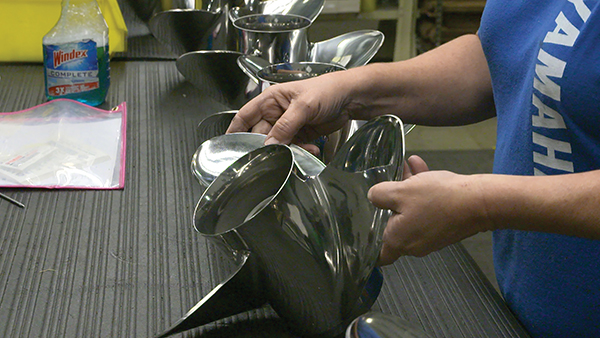
The Finished Product
Those propellers that pass inspection are sent to the Indianapolis plant to go through a battery of labor-intensive processes. There, workers manually grind the props with belt sanders, correct tiny voids with precision welds and detail the propellers to make the finish flawless.
The propellers are then placed into a giant vibrating tub filled with small ceramic cones to start the polishing process, followed by drag polishers with plastic media then precise measuring and tweaking with hammers to ensure they fall within the tight tolerances that are required before they receive a final polish before boxing.
Once you see all the detailed work it takes to construct a Yamaha propeller, you’ll never again wonder why propellers cost as much as they do.
Back to Blue Life
When touring the new state-of-the-art Yamaha Marine Precision Propellers Inc. (YPPI) facility in Greenfield, Indiana, it’s hard to believe its origin can be traced back to a two-car garage in Indianapolis in 1969 where founder Jim Booe would repair props and also tweak them to make boats go faster. Later, he began making his own quality propeller and Yamaha Marine became one of his best customers. When Yamaha acquired Precision Propeller Inc. in 2008, it built on the work previously done and began a steady progression of modernization that took a quantum leap when it opened the Greenfield facility in July 2021. The Indianapolis plant is still operating and while the manufacturing — including the foundry — transitioned to the new facility, it’s still used to put the final touches on the propeller and prepare them for shipping.
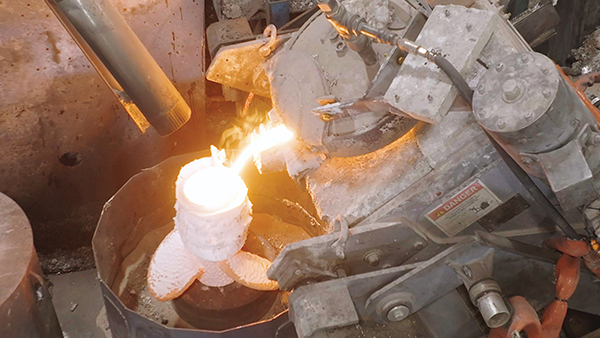
Robots do the Dirty, Difficult, Dangerous Jobs
The biggest change at the new $18 million, 55,000 square foot facility is its increased use of robotics to handle many of the potentially hazardous tasks such as pouring the 3,000-degree molten stainless steel from the crucible into the ceramic molds.
When most people hear the word robots, they assume the motivation to employ them is to replace human workers but in this case, it helped Yamaha up its production of propellers from 60,000 a year to more than 100,000 while achieving better tolerances that reduce waste and ultimately save the consumer money. Instead of laying off employees, Yamaha has been hiring more workers and operates 24 hours a day, five days a week, cranking out 300 different models of propellers. YPPI General Manager Batuhan Ak explains the other motives for switching some processes to automation, “The whole plant here was built with the philosophy of eliminating the 3Ds. We wanted to get rid of the difficult jobs, the dirty jobs and the dangerous jobs.”
Looking at just the pouring process illustrates how greater efficiency is achieved with the automated process. Previously, YPPI used two induction furnaces. One held 150 pounds of molten stainless steel while the smaller one held 65 pounds. Between the two, there was enough liquid metal to make seven propellers at a time. For smaller propellers, when the metal was hot enough, two silver-suited workers would lift a crucible filled with molten metal and manually pour it into the ceramic propeller molds. After which, another insulated employee would move the glowing mold and place it on a cooling rack where an open-ended barrel would be placed over it to contain the radiant heat to foster a consistent cooling environment. The larger props were filled with a manually tiltable crucible. Then, there would be a 15-minute reset while metal ingots were loaded and heated to 3,000 degrees.
The new auto-pour system holds several thousand pounds of molten stainless steel alloy and as the level goes down, more can be added without pausing. The new metal takes about 15 seconds to come up to the correct temperature so it can continuously operate. The system is also safer for employees since it eliminates manual pouring for the Yamaha props.
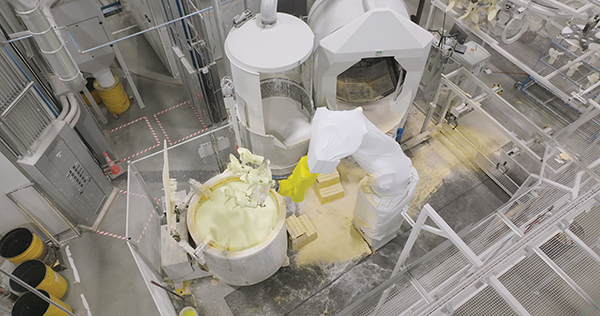
The Ancient Art Made Modern
Only stainless steel propellers are made and finished at the two Indiana facilities and the construction technique used is similar to the lost wax process Egyptians used 5,000 years ago to make jewelry. Although robotics makes sense for some tasks, many of the jobs require skilled workers with many years of experience to accomplish. The manufacturing process starts by injecting melted wax into an aluminum mold where it’s put under 200 pounds
of pressure to help fill the voids and ensure the perfect density of the hubs and blades, which are molded separately. After the wax cools, the mold is cracked opened and the formed components are inspected and any extraneous wax remnants are scraped off.
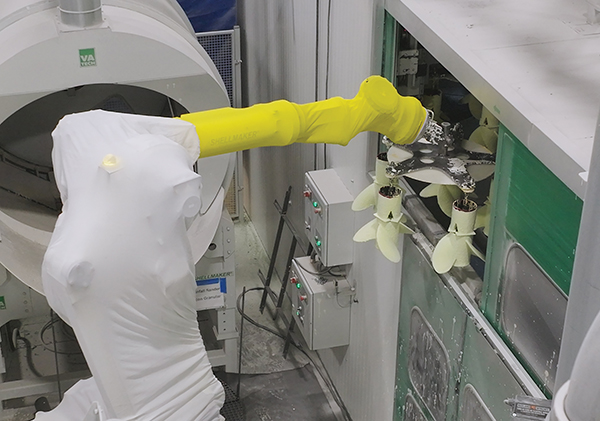
It Takes a Very Skilled Village
The blades are then joined to the hub and this is an especially critical step that requires a skilled hand. The assembler uses a soldering iron to join the base of the blade to the hub but if it’s applied a fraction of a second too long the blade or hub will be ruined. The positioning of the blades onto the hub must be perfect. When the blades are in place, black goop is applied to the base and it’s smoothed with a heated ball and the excess is scraped off. If the seams aren’t perfect, it will show up when the metal is poured and the propeller will have balance issues and could be scrapped.
Next, a pour cup is attached, which acts as a funnel, and the assembly is given several baths to clean the surfaces inside and out. The first appearance of robots appears at the dipping station where five wax propellers at a time are dipped into a primer slurry and turned and rotated like an amusement park ride to ensure an even coating before being given a zircon flour (milled sand) shower to start the build-up process of creating a ceramic shell. Four more layers of slurry and silica sand are added to increase thickness with periods of drying in between and after. This process used to be done by hand, which could cause inconsistencies and could take days but now can be done in 24 hours.
The dried ceramic shell still contains the wax, which must be melted away in an autoclave to create a void where the molten metal will fill. Then the ceramic mold is heated in preparation for the pouring.
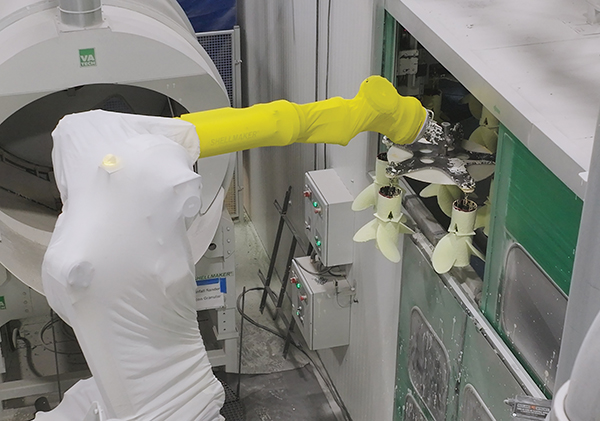.jpg)
It’s 3,000 degrees but it’s a Dry Heat
Next, comes the automated pouring sequence previously described. The entire process is monitored by computers and the progress of the line is displayed on giant screens throughout the plant including the reception area. This allows everyone to observe, at a glance, if progress is keeping pace with projections and where problems may exist. It even shows the angle of the last pour from the crucible, which lets supervisors know how much molten metal is remaining. They can even monitor the process remotely by smartphone to always stay in the loop.
Then, the newly poured propellers are sent to the cooling station and later the ceramic shell is removed by pneumatic hammering before being sand-blasted to remove any remnants, and then the pouring cup is cut off. According to Ak, the manual sand blasting station is one of the next scheduled processes to be automated since it’s one of those dirty jobs they are seeking to eliminate.
What’s left is a grey propeller with a dull finish since it’s covered with a coat of “free iron” which will be removed by abrading it with stainless steel balls.
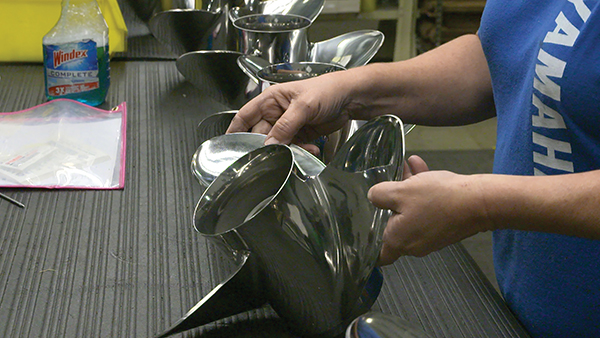
The Finished Product
Those propellers that pass inspection are sent to the Indianapolis plant to go through a battery of labor-intensive processes. There, workers manually grind the props with belt sanders, correct tiny voids with precision welds and detail the propellers to make the finish flawless.
The propellers are then placed into a giant vibrating tub filled with small ceramic cones to start the polishing process, followed by drag polishers with plastic media then precise measuring and tweaking with hammers to ensure they fall within the tight tolerances that are required before they receive a final polish before boxing.
Once you see all the detailed work it takes to construct a Yamaha propeller, you’ll never again wonder why propellers cost as much as they do.
Back to Blue Life